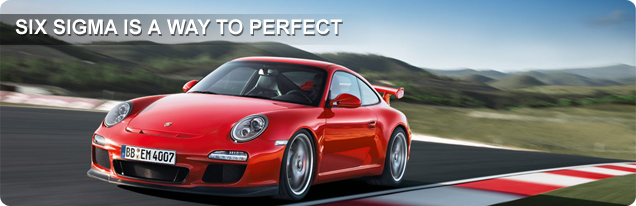
Enterprise wide Deployment
1. Enterprise View
a. Value of six sigma
Understand the organizational value of six sigma and its philosophy, goals, and definition. (Comprehension)
b. Business systems and processes
Understand and distinguish interrelationships between business systems and processes. (Comprehension)
c. Process inputs, outputs, and feedback
Describe how process inputs, outputs, and feedback of the system impact the enterprise system as a whole. (Comprehension)
2. Leadership
a. Enterprise leadership
Understand leadership roles in the deployment of six sigma (e.g. resources, organizational structure). (Comprehension)
b. Six sigma roles and responsibilities
Understand the roles/responsibilities of black belt, master black belt, green belt, champion, executive, and process owners. (Comprehension)
3. Organizational Goals and Objectives
• Understand key drivers for business; understand key metrics/scorecards
a. Linking projects to organizational goals
Describe the project selection process including knowing when to use six sigma improvement methodology (DMAIC) as opposed to other problem-solving tools, and confirm link back to organizational goals. (Comprehension)
b. Risk analysis
Describe the purpose and benefit of strategic risk analysis (e.g., strengths, weaknesses, opportunities, threats (SWOT), scenario planning), including the risk of optimizing elements in a project or process resulting in suboptimizing the whole. (Comprehension)
c. Closed-loop assessment/knowledge management
Document the objectives achieved and manage the lessons learned to identify additional opportunities. (Comprehension)
4. History of Organizational Improvement/Foundations of Six Sigma
• Improvement/Foundations of Six Sigma
Understand origin of continuous improvement tools used in six sigma (e.g., Deming, Juran, Shewhart, Ishikawa, Taguchi). (Comprehension)
Business Process Management
1. Process vs. Functional View
a. Process elements
Understand process components and boundaries. (Analysis)
b. Owners and stakeholders
Identify process owners, internal and external customers, and other stakeholders.(Analysis)
c. Project management and benefits
Understand the difference between managing projects and maximizing their benefits to the business. (Analysis)
d. Project measures
Establish key performance metrics and appropriate project documentation. (Analysis)
2. Voice of the Customer
a. Identify customer
Segment customers as applicable to a particular project; list specific customers impacted by project within each segment; show how a project impacts internal and external customers; recognize the financial impact of customer loyalty. (Analysis)
b. Collect customer data
Use various methods to collect customer feedback (surveys, focus groups, interviews, observation, etc.) and understand the strengths and weaknesses of each approach; recognize the key elements that make surveys, interviews, and other feedback tools effective; review questions for integrity (bias, vagueness, etc.). (Application)
c. Analyze customer data
Use graphical, statistical, and qualitative tools to understand customer feedback. (Analysis)
d. Determine critical customer requirements
Translate customer feedback into strategic project focus areas using quality function deployment (QFD) or similar tools, and establish key project metrics that relate to the voice of the customer and yield process insights. (Analysis)
3. Business Results
a. Process performance metrics
Calculate DPU, RTY, and DPMO sigma levels; understand how metrics propagate upward and allocate downward; compare and contrast capability, complexity, and control; manage the use of sigma performance measures (e.g., PPM, DPMO, DPU, RTY, COPQ) to drive enterprise decisions. (Analysis)
b. Benchmarking
Understand the importance of benchmarking. (Knowledge)
c. Financial benefits
Understand and present financial measures and other benefits (soft and hard) of a project; understand and use basic financial models (e.g., NPV, ROI); describe, apply, evaluate, and interpret cost of quality concepts, including quality cost categories, data collection, reporting, etc. (Application)
Project Management
1. Project Charter and Plan
a. Charter/plan elements
Compare, select, and explain elements of a project¡¯s charter and plan. (Analysis)
Planning tools
Plan the project using tools such as Gantt chart, PERT chart, planning trees, etc. (Application)
b. Project documentation
Create data-driven and fact-driven project documentation using spreadsheets, storyboards, phased reviews, management reviews, presentations to the executive team, etc. (Synthesis)
c. Charter negotiation
Create and negotiate the charter, including objectives, scope, boundaries, resources, project transition, and project closure. (Analysis)
2. Team Leadership
a. Initiating teams
Know the elements of launching a team and why they are important: clear purpose, goals, commitment, ground rules, roles and responsibilities of team members, schedules, support from management, and team empowerment. (Application)
b. Selecting team members
Select team members who have appropriate skills sets (e.g., self-facilitation, technical/subject-matter expertise), and create teams with appropriate numbers of members and representation. (Application)
c. Team stages
Facilitate the stages of team evolution, including forming, storming, norm, performing, adjourning, and recognition. (Application)
3. Team Dynamics and Performance
a. Team-building techniques
Recognize and apply the basic steps in team building: goals, roles and responsibilities, introductions, and both stated and hidden agendas. (Synthesis)
b. Team facilitation techniques
Apply coaching, mentoring, and facilitation techniques to guide a team and overcome problems such as overbearing, dominant, or reluctant participants; the unquestioned acceptance of opinions as facts; group-think; feuding; floundering; the rush to accomplishment; attribution; discounts and plops; digressions and tangents; etc. (Application)
c. Team performance evaluation
Measure team progress in relation to goals, objectives, and metrics that support team success. (Analysis)
d. Team tools
Define, select, and apply team tools such as nominal group technique, force-field analysis, multivoting, and conversion/diversion. (Application)
4. Change Agent
a. Managing change
Understand and apply techniques for facilitating or managing organizational change through change agent methodologies. (Application)
b. Organizational roadblocks
Understand the inherent structures of an organization (e.g., its cultures and constructs) that present basic barriers to improvement; select and apply techniques to overcome them. (Application)
c. Negotiation and conflict resolution techniques
Define, select, and apply tools such as consensus techniques, brainstorming, effort/impact, multivoting, interest-based bargaining to help conflicting parties (e.g., departments, groups, leaders, staff) recognize common goals and how to work together to achieve them. (Application)
d. Motivation techniques
Define, select, and apply techniques that support and sustain team member participation and commitment. (Application)
e. Communication
Use effective and appropriate communication techniques for different situations to overcome organizational
5. Management and planning tools
• Define, select, and use:
i. affinity diagrams;
ii. interrelationship digraphs;
iii. tree diagrams;
iv. prioritization matrices;
v. matrix diagrams;
vi. process decision program charts (PDPC);
vii. activity network diagrams. (Application)
Six Sigma Improvement Methodology and Tools¡ªDefine
a. Project Scope
Determine project definition/scope using Pareto charts, top-level process (macro) maps, etc. (Synthesis)
b. Metrics
Establish primary and consequential metrics (quality, cycle time, cost). (Analysis)
c. Problem Statement
Develop problem statement, including baseline and improvement goals. (Synthesis)
Six Sigma Improvement Methodology and Tools¡ªMeasure
1. Process Analysis and Documentation
a. Tools
Develop and review process maps, written procedures, work instructions, flowcharts, etc. (Analysis)
b. Process inputs and outputs
Identify process input variables and process output variables, and document their relationships through cause-and-effect diagrams, relational matrices, etc. (Evaluation)
2. Probability and Statistics
a. Drawing valid statistical conclusions
Distinguish between enumerative (descriptive) and analytical (inferential) studies, and distinguish between a population parameter and a sample statistic. (Evaluation)
b. Central limit theorem and sampling distribution of the mean Define the central limit theorem and understand its significance in the application of inferential statistics for confidence intervals, control charts, etc. (Application)
c. Basic probability concepts
Describe and apply concepts such as independence, mutually exclusive, multiplication rules, complementary probability, joint occurrence of events, etc. (Application)
3. Collecting and Summarizing Data
a. Types of data
Identify, define, classify, and compare continuous (variables) and discrete (attributes) data, and recognize opportunities to convert attributes data to variables measures. (Evaluation)
b. Measurement scales
Define and apply nominal, ordinal, interval, and ratio measurement scales. (Application)
c. Methods for collecting data
Define and apply methods for collecting data such as check sheets, coding data, automatic gauging, etc. (Evaluation)
d. Techniques for assuring data accuracy and integrity
Define and apply techniques for assuring data accuracy and integrity such as random sampling, stratified sampling, sample homogeneity, etc. (Evaluation)
e. Descriptive statistics
Define, compute, and interpret measures of dispersion and central tendency, and construct and interpret frequency distributions and cumulative frequency distributions. (Evaluation)
[NOTE: Measures of the geometric and harmonic mean will not be tested.]
f. Graphical methods
Depict relationships by constructing, applying, and interpreting diagrams and charts such as stem-and-leaf plots, box-and whisker plots, run charts, scatter diagrams, etc., and depict distributions by constructing, applying, and interpreting diagrams such as histograms, normal probability plots, Weibull plots, etc. (Evaluation)
4. Properties and Applications of Probability Distributions
a. Distributions commonly used by black belts
Describe and apply binomial, Poisson, normal, chi-square, Student¡¯s t, and F distributions. (Evaluation)
b. Other distributions
Recognize when to use hypergeometric, bivariate, exponential, lognormal, and Weibull distributions. (Application)
5. Measurement Systems
a. Measurement methods
Describe and review measurement methods such as attribute screens, gauge blocks, calipers, micrometers, optical comparators, tensile strength, titration, etc. (Comprehension)
b. Measurement system analysis
Calculate, analyze, and interpret measurement system capability using repeatability and reproducibility, measurement correlation, bias, linearity, percent agreement, precision/tolerance (P/T), precision/total variation (P/TV), and use both ANOVA and
control chart methods for nondestructive, destructive, and attribute systems. (Evaluation)
c. Metrology
Understand traceability to calibration standards, measurement error, calibration systems, control and integrity of standards and measurement devices (Comprehension)
6. Analyzing Process Capability
a. Designing and conducting process capability studies
Identify, describe, and apply the elements of designing and conducting process capability studies, including identifying characteristics, identifying specifications/tolerances, developing sampling plans, and verifying stability and normality (Evaluation)
b. Calculating process performance vs. specification
Distinguish between natural process limits and specification limits, and calculate process performance metrics such as percent defective (Evaluation)
c. Process capability indices
Define, select, and calculate Cp, Cpk, and assess process capability (Evaluation)
d. Process performance indices
Define, select, and calculate Pp, Ppk, Cpm, and assess process performance (Evaluation)
e. Short-term vs. long-term capability
Understand the assumptions and conventions appropriate when only short-term data are collected and when only attributes data are available; understand the changes in relationships that occur when long-term data are used; interpret relationships between long-term and short-term capability as it relates to technology and/or control problems. (Evaluation)
f. Non-normal data transformations (process capability for non-normal data) Understand the cause of non-normal data and determine when it is appropriate to transform. (Application)
g. Process capability for attributes data
Compute sigma level and understand its relationship to Ppk (Application)
Six Sigma Improvement Methodology and Tools¡ªAnalyze
1. Exploratory Data Analysis
a. Multi-vari studies
Use multi-vari studies to interpret the difference between positional, cyclical, and temporal variation; design sampling plans to investigate the largest sources of variation; create and interpret multi-vari charts. (Application)
b. Measuring and modeling relationships between variables
i. Simple and multiple least-squares linear regression
Calculate the regression equation; apply and interpret hypothesis tests for regression statistics; use the regression model for estimation and prediction, and analyze the uncertainty in the estimate. (Models that have nonlinear parameters will not be tested.) (Evaluation)
ii. Simple linear correlation
Calculate and interpret the correlation coefficient and its confidence interval; apply and interpret a hypothesis test for the correlation coefficient; understand the difference between correlation and causation. (Serial correlation will not be tested.) (Evaluation)
iii. Diagnostics
Analyze residuals of the model. (Analysis)
2. Hypothesis Testing
a. Fundamental concepts of hypothesis testing
i. Statistical vs. practical significance
Define, compare, and contrast statistical and practical significance. (Evaluation)
ii. Significance level, power, type I and type II errors
Apply and interpret the significance level, power, type I and type II errors of statistical tests. (Evaluation)
iii. Sample size
Understand how to calculate sample size for any given hypothesis test. (Application)
b. Point and interval estimation
Define and interpret the efficiency and bias of estimators; compute, interpret, and draw conclusions from statistics such as standard error, tolerance intervals, and confidence intervals; understand the distinction between confidence intervals and prediction intervals.(Analysis)
c. Tests for means, variances, and proportions
Apply hypothesis tests for means, variances, and proportions, and interpret the results. (Evaluation)
d. Paired-comparison tests
Define, determine applicability, and apply paired-comparison parametric hypothesis tests, and interpret the results. (Evaluation)
e. Goodness-of-fit tests
Define, determine applicability, and apply chi-square tests and interpret the results. (Evaluation)
f. Analysis of variance (ANOVA)
Define, determine applicability, and apply ANOVAs and interpret the results. (Evaluation)
g. Contingency tables
Define, determine applicability, and construct a contingency table and use it to determine statistical significance. (Evaluation)
h. Nonparametric tests
Define, determine applicability, and construct various nonparametric tests including Mood¡¯s Median, Levene¡¯s test, Kruskal-Wallis, Mann-Whitney, etc. (Analysis)
Six Sigma Improvement Methodology and Tools¡ªImprove
1. Design of Experiments (DOE)
a. Terminology
Define independent and dependent variables, factors and levels, response, treatment, error, and replication (Comprehension)
b. Planning and organizing experiments
Describe and apply the basic elements of experiment planning and organizing, including determining the experiment objective; selecting factors, responses, and measurement methods; choosing the appropriate design, etc. (Evaluation) ASQ Certified Six Sigma Black Belt BOK (continued)
c. Design principles
Define and apply the principles of power and sample size, balance, replication, order, efficiency, randomization and blocking, interaction, and confounding. (Application)
d. Design and analysis of one-factor experiments
Construct these experiments such as completely randomized, randomized block, and Latin square designs, and apply computational and graphical methods to analyze and evaluate the significance of results. (Evaluation)
e. Design and analysis of full-factorial experiments
Construct these experiments and apply computational and graphical methods to analyze and evaluate the significance of results. (Evaluation)
f. Design and analysis of two-level fractional factorial experiments
Construct experiments (including Taguchi designs) and apply computational and graphical methods to analyze and evaluate the significance of results; understand limitations of fractional factorials due to confounding. (Evaluation)
g. Taguchi robustness concepts
Apply Taguchi robustness concepts and techniques such as signal-to-noise ratio, controllable and noise factors, and robustness to external sources of variability. (Analysis)
h. Mixture experiments
Construct these experiments and apply computational and graphical methods to analyze and evaluate the significance of results. (Analysis)
2. Response Surface Methodology
a. Steepest ascent/descent experiments
Construct these experiments and apply computational and graphical methods to analyze the significance of results. (Analysis)
b. Higher-order experiments
Construct experiments such as CCD, Box-Behnken, etc., and apply computational and graphical methods to analyze the significance of results. (Analysis)
3. Evolutionary Operations (EVOP)
• Understand the application and strategy of EVOP. (Comprehension)
Six Sigma Improvement Methodology and Tools¡ªControl
1. Statistical Process Control (SPC)
a. Objectives and benefits
Understand objectives and benefits of SPC (e.g., controlling process performance, distinguishing special from common causes). (Comprehension)
b. Selection of variable
Select critical characteristics for monitoring by control chart. (Application)
c. Rational subgrouping
Define and apply the principle of rational subgrouping. (Application)
d. Selection and application of control charts
Identify, select, construct, and apply the following types of control charts: x-bar and
R, x-bar and s, individual and moving range (ImR / XmR), median, p, np, c, and u. (Application)
e. Analysis of control charts
Interpret control charts and distinguish between common and special causes using rules for determining statistical control. (Analysis)
f. PRE-control
Define and explain PRE-control and perform PRE-control calculations and analysis. (Analysis)
2. Advanced Statistical Process Control
• Understand appropriate uses of short-run SPC, EWMA, CuSum, and moving average (Comprehension)
3. Lean Tools for Control
• Apply appropriate lean tools (e.g., 5S, visual factory, kaizen, kanban, poka-yoke, total productive maintenance, standard work) as they relate to the control phase of DMAIC (Application) [NOTE: The use of lean tools in other areas of DMAIC is covered in section
4. Measurement System Re-analysis
• Understand the need to improve measurement system capability as process capability improves; evaluate the use of control measurement systems (e.g., attributes, variables, destructive); and ensure that measurement capability is sufficient for its intended use. (Evaluation)
Lean Enterprise
1. Lean Concepts
a. Theory of constraints
Describe the theory of constraints (Comprehension)
b. Lean thinking
Describe concepts such as value, value chain, flow, pull, perfection, etc. (Comprehension)
c. Continuous flow manufacturing (CFM)
Describe the concept CFM. (Comprehension)
d. Nonvalue-added activities
Identify these activities in terms inventory, space, test inspection, rework, transportation, storage, etc. (Application)
e. Cycle-time reduction
Describe how cycle-time reduction can be used to identify defects and nonvalue-added activities using kaizen-type methods to reduce waste of space, inventory, labor, and distance. (Comprehension)
2. Lean Tools
• Define, select, and apply tools such as visual factory, kanban, poka-yoke, standard work, SMED, etc., in areas outside of DMAIC Control. (Application) [NOTE: The use of lean tools in DMAIC-Control is covered in section VIII. C.]
3. Total Productive Maintenance (TPM)
• Understand the concept of TPM. (Comprehension)
Design for Six Sigma (DFSS)
1. Quality Function Deployment (QFD)
Analyze a completed QFD matrix. (Analysis)
2. Robust Design and Process
a. Functional requirements
Understand functional requirements of a design. (Comprehension)
b. Noise strategies
Develop a robust design using noise strategies. (Application)
c. Tolerance design
Understand the concepts of tolerance design and statistical tolerance. (Analysis)
d. Tolerance and process capability
Calculate tolerances using process capability data. (Analysis)
3. Failure Mode and Effects Analysis (FMEA)
Understand the terminology, purpose, and use of scale criteria (RPN) and be able to apply it to a process, product, or service; understand the distinction between and interpret data associated with DFMEA and PFMEA (Analysis)
4. Design for X (DFX)
Understand design constraints such as design for cost, design for manufacturability and producibility, design for test, design for maintainability, etc. (Comprehension)
5. Special Design Tools
Understand the concept of special design tools such as the theory of inventive problem solving (TRIZ), axiomatic design (conceptual structure robustness), etc. (Knowledge)
Six Levels of Cognition Based on Bloom¡¯s Taxonomy (1956)
• In addition to content specifics, the subtext detail also indicates the intended complexity level of the test questions for that topic. These levels are based on ¡°Levels of Cognition¡± (from Bloom¡¯s Taxonomy, 1956) and are presented below in rank order, from least complex to most complex.
a. Knowledge Level
(Also commonly referred to as recognition, recall, or rote knowledge.) Be able to remember or recognize terminology, definitions, facts, ideas, materials, patterns, sequences, methodologies, principles, etc.
b. Comprehension Level
Be able to read and understand descriptions, communications, reports, tables, diagrams, directions, regulations, etc.
c. Application Level
Be able to apply ideas, procedures, methods, formulas, principles, theories, etc., in job-related situations.
d. Analysis
Be able to break down information into its constituent parts and recognize the parts¡¯ relationship to one another and how they are organized; identify sublevel factors or salient data from a complex scenario.
e. Synthesis
Be able to put parts or elements together in such a way as to show a pattern or structure not clearly there before; identify which data or information from a complex set are appropriate to examine further or from which supported conclusions can be drawn.
f. Evaluation
Be able to make judgments regarding the value of proposed ideas, solutions, methodologies, etc., by using appropriate criteria or standards to estimate accuracy, effectiveness, economic benefits, etc.
» More Information